EMI Shielding Products
- Custom Gasket Fabrication
- Connector Gaskets
- Bonded O Ring
- Custom Gaskets
- Conduct-O-Knit Knitted Wire Mesh
- Conduct-O-Seal Combo Gasket
- Conduct-O-Elastomer
- Conduct-O-Seal Oriented Wire in Silicone Gasket Material
- Conduct-O-Mesh Tape
- Conduct-O-Foam
- Conduct-O-Bond
- Optical Filters For Electronic Displays
- Shielded Vent Panels
- 300 Series
Popular Materials for EMI Shields and Gaskets
Three popular shielding metals are commonly used when creating EMI shielding. When determining materials for shields, people must navigate between extremes: cost and performance. If someone skimps on costs, performance will inevitably suffer as well.
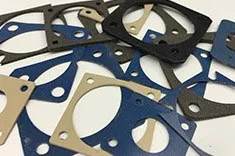
As you begin to make a budget, you will have to make important decisions about:
- Galvanic compatibility
- Conductivity
- Corrosion resistance to the operation environment
- Material thickness
- Enclosure geometry
- Application frequencies
- Short/long term production quantities
- Packaging
- Assembly
One way to help save on costs is to use one of three EMI shielding materials.
Pre-tin plated steel: this material is a great low-cost solution that does not cut many corners. It works great from lower frequencies on the KHz range through frequencies in the lower GHz range. Pre-tin steel offers strong corrosion resistance for the steel that allows it to prevent rust. Lastly, it has excellent solderable surface.
Copper alloy 770: this material is commonly referred to as alloy 770, and it is a copper, zinc, and nickel alloy used in EMI shielding and EMI gaskets. It is most frequently used for its corrosion resistance. This alloy is widely used in MRI related applications that require no magnetic materials.
EMI Shielding
Aluminum: the material does have fabrication challenges, but it is still a great choice because it is non-ferrous, has excellent strength-to-weight ratios, and it is highly conductive. When compared with copper, aluminum is nearly 60% more conductive. If using this material, engineers must pay special attention to galvanic corrosion and oxidation.
Related Reading:- EMI Shielding and the MilitaryOne of the most technical industries in the United States is the defense industry. They are continually pushing the boundaries and advancing electronic systems, such as ultramodern communication devices and vehicles.
- Design Tips for EMI Shielding Corrosion Resistance
- EMI and Consumer Products
- Spliced and Molded EMI Shielding Gaskets