EMI Shielding Products
- Custom Gasket Fabrication
- Connector Gaskets
- Bonded O Ring
- Custom Gaskets
- Conduct-O-Knit Knitted Wire Mesh
- Conduct-O-Seal Combo Gasket
- Conduct-O-Elastomer
- Conduct-O-Seal Oriented Wire in Silicone Gasket Material
- Conduct-O-Mesh Tape
- Conduct-O-Foam
- Conduct-O-Bond
- Optical Filters For Electronic Displays
- Shielded Vent Panels
- ESC Board Level Shielding
- 300 Series
Die Cut EMI Gaskets and There Benefits
Die cut gaskets that are made for EMI shielding and other applications are customizable, cost-effective, and most importantly, they are reliable. Die cutting, as a manufacturing technique combines proven technologies and efficient gasket fabrication. Although different cutting techniques exist, to meet varied needs, most cutting methods include two core components: a metal cutting tool (a die) and a cutting machine. If you are in the market for connector gaskets, you should consider die cutting as an option for manufacturing. We use the method to produce a wide array of different types of seals and insulation.
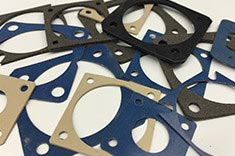
Die cutting quickly creates gasket sizes that have tight tolerances. Part manufacturing volumes range from prototyping to high-volume production runs. When the cutting process is finished, parts have clean edges. They can also be built with bolt holes created to exact radii.
Of all the reasons to consider die cut EMI gaskets and EMI shields, one is valued above all other.
Low Setup Cost: because of rotary and flatbed equipment, setup costs are reduced when using die cutting. Automation in handling systems replaces slow, manual material feeding. Machines are built with vision systems that support part alignment and registration. The type of die used for cutting can also help to drive down cutting costs. Through carefully balancing tool type, material type, gasket die cutting technique, and part feature, it is possible for individuals to source soft-effective die cut gaskets.
EMI Gaskets
- Spliced and Molded EMI Shielding Gaskets
EMI shielding gaskets are sold in several different materials with a limitless amount of sizes and shapes. Typically, base materials are made from fluorosilicone or silicon that has fillers like silver, silver-plated aluminum, and nickel-plated graphite. These conductive elastomers are one of the most versatile products for EMI shielding gaskets.
- Popular Materials for EMI Shields and Gaskets
- Manufacturing Options for EMI Shielding