EMI Shielding Products
- Custom Gasket Fabrication
- Connector Gaskets
- Bonded O Ring
- Custom Gaskets
- Conduct-O-Knit Knitted Wire Mesh
- Conduct-O-Seal Combo Gasket
- Conduct-O-Elastomer
- Conduct-O-Seal Oriented Wire in Silicone Gasket Material
- Conduct-O-Mesh Tape
- Conduct-O-Foam
- Conduct-O-Bond
- Optical Filters For Electronic Displays
- Shielded Vent Panels
- ESC Board Level Shielding
- 300 Series
Three Common Shielding Metals
It is essential for electronics engineers to carefully consider balancing cost and performance when it comes to constructing EMI and RFI shielding. Tipping the scale too far one way has negative consequences. Being aware of the design process allows for individuals to make critical decisions that help guide the decision-making process.
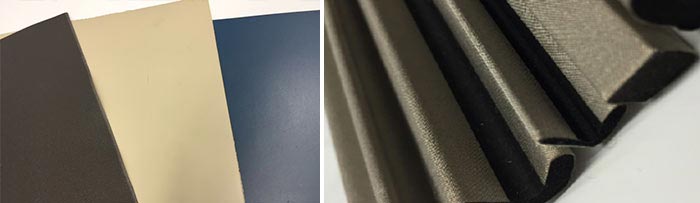
People need to be mindful of:
- Costs (tooling costs/part price)
- Conductivity
- Application environment
- Galvanic compatibility
- Application frequencies
- Material thickness
- Enclosure geometry
- Long vs. short term production quantities
Each of the above factors affects cost, packaging, assembly, and time of construction.
Of all the fundamental and crucial decisions an engineer can make, material selection is amongst the most important. The materials used for RFI and EMI shielding have a direct effect on the application performance and the cost of the project. We offer a comprehensive selection of materials to meet the strict demands of our customers.
EMI Shielding
There are several popular metals that are used to create RFI Shielding and EMI Shielding. These popular metals include:
Pre-tin plated steel: this metal is ideal for low-cost constructions that operate in low frequencies in the kHz range. They also work well for low frequencies in the GHz range. Tin plating offers extra corrosion resistance that prevents rusting.
Copper alloy 770: this alloy is commonly referred to simply as alloy 770. It is frequently used because of its strong corrosion resistance properties. Engineers like this material for work in the mid kHz range and mid GHz range.
Aluminum: the metal presents several fabrication challenges, but it is still an excellent application that requires non-ferrous properties. It has a high strength to weight ratio, and it is highly conductive.
- The Science of ShieldingEMI shielding gaskets are placed between the shield housing and the mating surface of the electronic device. In this position they can properly block the incoming and outgoing waves of EMI radiation.
- Shielding Gaskets and Corrosion
- Selection of Seal Cross Section