EMI Shielding Products
- Custom Gasket Fabrication
- Connector Gaskets
- Bonded O Ring
- Custom Gaskets
- Conduct-O-Knit Knitted Wire Mesh
- Conduct-O-Seal Combo Gasket
- Conduct-O-Elastomer
- Conduct-O-Seal Oriented Wire in Silicone Gasket Material
- Conduct-O-Mesh Tape
- Conduct-O-Foam
- Conduct-O-Bond
- Optical Filters For Electronic Displays
- Shielded Vent Panels
- 300 Series
Choosing Between Molding and Splicing
EMI shielding and RFI shielding gaskets come in two main types: molded gaskets and spliced gaskets. Both styles come in a wide, almost endless range of shapes, sizes, and materials. You will most commonly find them constructed from a base material of fluorosilicone or silicone. In most cases, a combination of conductive fillers is added during production. When it comes to EMI shielding and RFI shielding, conductive elastomers are highly regarded as the most versatile products. Manufacturers recognized that the two key processes of creating gaskets are molding and splicing. How do you know which is right for your business and application?
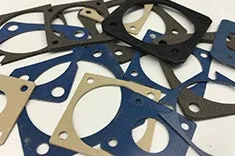
Gasket Splicing creates O-rings by cutting materials to proper lengths and then fusing the ends. The process uses proprietary adhesives to create the strongest possible bond. Advantages include:
- Hollow profiles
- Modified Designs
- Standard size options
- Quick turn parts
- Small tooling cost
It is important to keep in mind that splicing limits the complexity of singular loops, and that they do not retain shapes like a molded O-ring.
Gasket Molding works by compressing uncured elastomers into a predesigned mold. When the process is finished, the material retains the shape of the mold. Advantages include:
- Creates complex parts
- Tighter tolerances than splicing
- Economical
- Works with small sizes
- Strong shape retention
EMI RFI Shielding
Molding is not compatible with hollow gaskets, which means that a molded gasket cannot have hollow cross-sections. Also, as length and diameter grow, so does the initial cost.
Related Reading
- Creating Fast & Small Electronics with RFI ShieldingElectronics are susceptible to interference from outside sources, and these devices also create their own EMI and RFI. To allow modern devices to work seamlessly, you need to acquire EMI RFI shielding.
- The Two Best Ways to Reduce EMI and RFI
- Weatherizing EMI Shielding and RFI Shielding